The characteristic of the reduced diameter extrusion is that the extruded blank is not in a closed state, and the axial force of the blank itself is used to press the blank into the mold to produce a reduced diameter, and the desired product is obtained. As a result, it is often the case that the metal is piled up, resulting in failure to produce normally. Figure 1 is a splined shaft with a modulus m = 1, a number of teeth z = 11, and a tooth angle α = 45°. Figure 2 shows the phenomenon of metal compaction that occurs during spline extrusion.
First, the problem analysis
The main reason for the metal being pressed during the shrinkage cold extrusion spline process is that the friction between the extrusion die and the extruded blank is too large during the extrusion process, which is sufficient to cause radial deformation of the extruded blank, and even extrusion. It is difficult to continue and produce metal piles. The factors affecting the metal compaction during the reduction and extrusion process are: the extrusion friction force, the extrusion force, the extrusion die, the blank, the deformation resistance, the deformation degree and the deformation speed generated during the extrusion process.
Second, the solution
1. Reduce friction
The friction reduction is mainly from the following points.
(1) Calculating the amount of squeezed diameter and reducing the diameter is the key to determine whether the diameter reduction can be carried out. According to practical experience, the extrusion diameter of the annealed billet is generally smaller than that of the unannealed or quenched billet. . If a metal pile is produced from the beginning of the test die extrusion, then it should be analyzed to calculate whether the squeezed diameter during the extrusion process is reasonable. According to the test, the maximum crushing diameter of the tempered billet and the non-annealed billet is 38%, but it is difficult to achieve this in actual production, and generally less than 25% of the diameter reduction range can be selected.
(2) Surface treatment and lubrication surface treatment are also the key factors to determine whether the diameter reduction extrusion can be carried out normally. If the extruded product produces a "bamboo" phenomenon during extrusion, this is due to excessive external friction. , causing the phenomenon that the metal flow velocity of the center layer is greater than that of the outer metal, or generating a pile in the middle of the extruded product. Then consider whether the surface treatment is reasonable, and the thickness of the phosphate film or oxalate film on the metal surface. At the same time, it is necessary to know whether the salt film adhesion layer on the metal surface is easy to fall off during the extrusion process and increase the frictional friction. The chemical treatment and reaction time of the surface treatment can be appropriately adjusted. At the same time, it is necessary to pay attention to the rational selection of lubricants, generally choose lubricants with low friction factor and low viscosity.
2. Improve the extrusion die to reduce the pressing force
The design of the extrusion die plays a decisive role in the reduction of the diameter extrusion. The improvement of the extrusion die can be started from the extrusion inlet, the guide angle α, the sizing working belt and the outlet, as shown in Fig. 3.
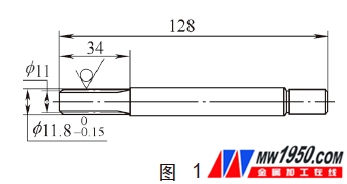
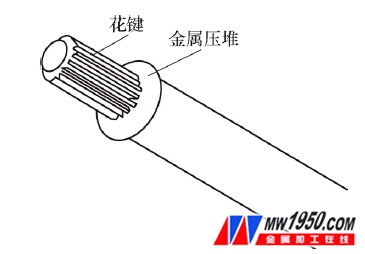
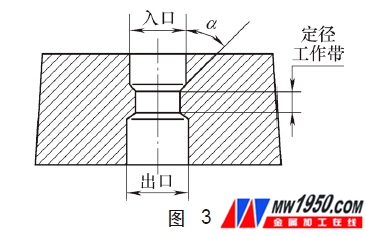
(1) The outer diameter of the mold inlet at the entrance of the mold should be different from the outer circle of the extruded spline blank. If the difference is large, the secondary deformation of the extruded blank is easy to occur, and the inlet does not play a good role. Reduced diameter extrusion is difficult. At the same time, the depth selection at the entrance should be reasonable. Practice has shown that it should increase according to the increase in the amount of reduction.
(2) The guiding angle of the mold guiding angle α is an important factor determining the pressing force of the reducing diameter. The design of the guiding angle of the mold should be reasonable. As the guiding angle increases, the pressing force will increase greatly, which may lead to the occurrence of the blank. To the deformation, the resulting metal is piled up during the extrusion process. However, the guide angle is too small, resulting in a short effective length of the spline. According to the production practice experience, the diameter of the extrusion guide angle α is selected from 25° to 45°, and the selection of the guide angle should also take into account the blank state and the blank type.
(3) Mold sizing work belt The length of the sizing working belt is also an important factor affecting the extrusion. The sizing working belt is too long, the pressing force will increase, and the shortness will make the metal product size unstable. If the crushing diameter is large, the length of the sizing working belt can be appropriately changed, but the dimensional accuracy of the extruded product must be ensured.
(4) Generally speaking, the exit of the mold should avoid friction between the extruded product and the exit of the mold, and the extrusion force is increased and the surface of the product is scratched. The design of the outer circle at the exit can not be arbitrary, and the outer circle will affect the service life of the mold. The size of the die exit can be selected according to the relevant information.
3. Adjust the uniformity of the hardness of the extruded billet
The hardness uniformity of the blank itself is also an important factor affecting the diameter reduction of the spline. If the billet produces uneven hardness during annealing or quenching and tempering, the extrusion force changes greatly during extrusion, the metal flow is uneven, and metal is prone to occur. Pressing situation. At the same time, the hardness of the blank is too high, which will affect the service life of the mold.
4. Improve comprehensive indicators
In general, the reduction of the diameter of the spline is a problem in the field of extrusion, therefore, the extrusion design requires a lot of considerations. For the design of the mold frame, it is reasonable to have a positioning device to ensure the concentricity during the extrusion process and reduce the pressing force. The precision of mold making is better, the materials should be reasonable, the surface roughness of the core should be small, and the die should be meticulous. The surface roughness of the blank is also relatively higher than other cold extrusion methods. The deformation speed control during the extrusion process has different degrees of influence on the reduction of the diameter.
Third, the conclusion
The application of the reduced diameter cold extrusion spline technology is not extensive. This paper carefully analyzes the various causes of metal compaction and discusses various methods for solving metal compaction. Practice shows that the above method is effective in actual production, and successfully solves the problem of metal piles generated during the cold extrusion process of different types of products.
   About the author: He Dakai, Design Manager of Guangdong Xinhai Construction Co., Ltd.
New student desks and chairs, you can lie down and lift
Two desktops have different options
The desktop adopts a secure rounded corner design,Hidden school bag hook.
The front edge of the seat and cushion adopts a wave design, which effectively reduces the pressure on the hips and waist.
School Furniture,Student desks and chairs,Nap Chair,Kids study desk,Student lunch desk.
FOSHAN CITY LESHUN RONGHUI FURNITURE CO.LTD , https://www.ronghuifurniture.com