1 INTRODUCTION Since Aisenberg and Chabot used the high-energy ion beam to deposit diamond-like carbon films at room temperature in 1971, there has been an upsurge of research and application development of diamond-like carbon films worldwide. The diamond-like film was prepared by a high-energy particle deposition method. Hydrocarbon gas is used to obtain the deposition method of carbon ion source, and the coating contains a large amount of hydrogen elements; while the deposition method using solid carbon (graphite) as the carbon ion source can obtain pure carbon coating. The diamond-like carbon film is usually amorphous or contains some nanocrystals. It is a mixture of diamond structure (SP3) and graphite structure (SP2). Its hardness, elastic modulus and other properties mainly depend on the content of SP3 structure. When SP3 ≥ 20%, hardness HV ≥ 2000, it is called diamond-like carbon film (DLC); when SP3 ≥ 70%, hardness HV ≥ 7000, it is called amorphous diamond carbon film because it belongs to tetrahedron diamond structure, It is also called amorphous tetrahedral diamond carbon film (ta-c). Amorphous diamond films have excellent properties such as high hardness, low coefficient of friction, and high thermal conductivity (see Table 1). They have a wide range of applications in the tool, gauge, and die manufacturing industries.
Table 1 Basic properties of amorphous diamond film Amorphous diamond film Diamond (natural, crystalline) SP3 content, % 70 to 95 100 Hardness, GPa 70 to 95 100 to 120 Density, g/cm3 3 to 3.5 3.515 Young's modulus, GPa ≥700 1000~1200 Resistivity,Wcm 108~1012 1016 Thermal conductivity,W/cm2·K 18 20 Optical bandgap,eV 2.6 5.45 Tap is a widely used tool in mechanical manufacturing. In recent years, the annual consumption of taps in our country is about 40 million sticks, each tap tapping life of 3.5 ~ 4m, that is, high-quality products, the actual use of the tap life is often less than 3m, and the foreign tap life (≥ 10m) compared to a wide gap. In order to make domestic taps reach or close to the foreign product level, many manufacturers have made unremitting efforts to explore the material composition, metallurgy quality, heat treatment, processing technology, knife-like structure design and surface coating and other aspects, but with little success. Therefore, the domestic industry generally believes that TiN, TiC, TiCN, CrN, TiAlN and other coatings on the life of the tap does not have much gain, many manufacturers almost gave up the tap coating efforts. Shaanxi Baina Technology Development Co., Ltd. analyzed the performance characteristics and process characteristics of nano-amorphous diamond coating, and considered this coating suitable for tapping applications. At present, PLATIT company in Switzerland has diamond-like film taps, but its film hardness is low. Shaanxi Baina Company applied amorphous diamond film to high-speed steel wire cones and developed high wear-resistant taps, and applied assessments at several factories. This article focuses on the analysis of high-speed steel plated amorphous diamond film, film/base bonding force, friction coefficient, wear resistance test results and high-speed steel cone after coating performance test and practical assessment results, and put forward reasonable application and give full play to the amorphous Diamond film potential measures. 2 test program test material test material and tap material are W6Mo5Cr4V2 high-speed steel, heat treatment according to conventional high-speed steel heat treatment specifications; test piece size f20 × 5mm, roughness Ra0.4, grinding machine taps M3 ~ M12. Coating process sample pretreatment: Acetone ultrasonic cleaning → Washing → Deionized water washing → Alcohol cleaning → Blow drying, stored in a dry container for use. An amorphous diamond film was deposited on the test piece using a filtered cathode vacuum arc ion coating machine (JM-1 amorphous diamond coating machine) developed by Shaanxi Bainar Science and Technology Development Co., Ltd. and deposited under optimized parameters for 30 minutes. Test project coating and substrate binding force determination: With the WS-2000 type coating adhesion scratch tester, according to JB/T 8554-1997 standards to determine the critical layer rupture or peeling load. Each test piece was measured three times and the average value was taken as the film/base binding force of the test piece. Friction coefficient measurement: Using UMT-2M (bolt type) friction tester, the coefficient of friction of the film and steel ball was measured by reciprocating motion. Ball diameter f4mm, hardness 62HRC, load 2N, relative movement speed 18mm/s. Abrasion resistance test: According to the ISO 3160-3:1993 standard, a wear test was performed on a MS-2 type friction tester. The grinding head is a f8mm steel ball with a hardness of 61-64HRC, loaded with 2N, and a rotational speed of 120r/min. The number of revolutions at which a visible continuous wear scar appears appears as the wear life. Tap performance test: According to JB/T 969-94 standard tapping life test on Z525 vertical drilling machine. The blank was made of 40Cr, hardness 200-220HB, spindle speed 366r/min, cutting speed 6.9m/min, clamping accuracy 0.05-0.09mm, and emulsion cooling. Table 2 Coefficients of friction of amorphous diamond film (ta-c) and commonly used coatings Coated substrate friction coefficient Parameter source ta-c W6Mo5Cr4V2 0.092 Cr12MoV 0.098 TiN tool steel 0.55 Siemens PLATIT company TiCN 0.2 TiAlCN 0.5 CrN 0.3 TiAlCN 0.25 3 Test results and analysis of friction coefficient of amorphous diamond film The friction coefficient of high-speed steel W6Mo5Cr4V2 and mold steel Cr12MoV after coating is shown in Table 2. Also listed are the friction coefficients of several commonly used coatings for comparison. It can be seen from Table 2 that the friction coefficient μ of the plated amorphous diamond film and the ball steel ball on high-speed steel and die steel is 0.092-0.098, which is much lower than that of common hard coating. There are also many reports that the friction coefficient of amorphous diamond film μ ≤ 0.08, after a deep understanding of the test conditions, that the test head is an emerald ball, so the friction coefficient is lower than the test results. Since the amorphous diamond film is composed of a carbon-homo isomer SP3 and SP2 hybrid bonding structure having a low friction coefficient, and the film is extremely uniform, dense, and smooth, the amorphous diamond film has a very low coefficient of friction. , can be seen as a coating with self-lubricating function. The binding force between the amorphous diamond film and the substrate The results of the determination of the binding force between the amorphous diamond film and the high-speed steel substrate are shown in Table 3. As can be seen from Table 3, the highest critical load in the specimen is 22.75N and the minimum is 17.15N. The average critical load of the three specimens is 19.15N. Since the thickness of the coating is about 150 to 200 nm, such a thin coating is measured on a WS-2000 scratch tester, and the resulting data tends to be low. The binding force of amorphous diamond films on silicon, glass and steel is relatively high, which is mainly related to the process of nucleation and growth of amorphous diamond films by subsurface implantation. If the coating is a purely surface process, it usually has a lower binding force.
Table 3 Coupling force of amorphous diamond film and high-speed steel substrate Specimen No No critical load Lc(N) Average critical load L c(N) 1 20.40 20.27 22.75 17.67 2 18.10 19.52 18.15 22.30 3 17.15 17.65 17.77 18.02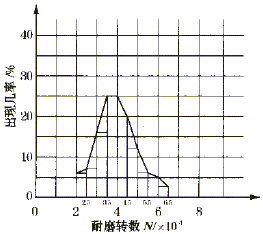
Fig. 1 Abrasion resistance of amorphous diamond film The wear resistance of the tracking plate of a high-speed steel cone coating (84 burners total) was tested on a MS-2 friction tester. The test results are shown in Figure 1. The minimum wear life of the coating was 21,410 rpm, the maximum life was 63,996 rpm, and the 30,000-50,000 rpm range accounted for 73.81%. This shows that the coating has good quality stability. The uncoated high-speed steel wear rotation is only about 200 rpm. Therefore, under the conditions of standard plug wear in the laboratory, the wear resistance of the high-speed steel plated amorphous diamond film increases by 106 to 319 times. Although the plated amorphous diamond film is very thin, its effect of improving the wear resistance is very remarkable. In general, the wear resistance of the coating depends mainly on the hardness of the coating, the coefficient of friction, the bonding force of the film, and the thickness of the film. Amorphous diamond film is a superhard film with a small friction coefficient. The film has a high bonding force and has high wear resistance despite the nanometer thickness. When we optimized the process, we found that if the film/base bonding force (critical load) is less than 10N, the wear resistance of the film is significantly worse. The results of the cutting performance test of the plated amorphous diamond film taps are shown in Table 4. The average cutting life of the amorphous diamond coated M6 tap was 5.6 times longer than that of the uncoated tap, and the mean cutting life of the coated M10 tap was 2.46 times longer than that of the uncoated tap. It can be seen that after tapping the amorphous diamond film on the tap, the service life of the tap can be effectively improved. It was also found in the test that the taps that failed in the wear mode had high cutting life, while the taps that failed in the chipping had shorter life spans. This shows that the wear resistance potential of amorphous diamond films can only be fully exerted when they fail due to wear.
Table 4 Cutting efficiency test results of plated amorphous diamond film taps No Tap size Coating life failure mode Number of holes (m) 1-1 M6 ta-c 186 1.674 Wear 1-2 M6 ta-c 187 1.683 Wear 1-3 M6 Ta-c 54 0.486 chipping 1-4 M6 ta-c 112 1.008 chipping 1-5 M6 ta-c 87 0.783 chipping, wear 2-1 M6 uncoated 30 0.27 chipping 2-2 M6 uncoated 20 0.18 collapse Blade 2-3 M6 Uncoated 8 0.072 Bladed 2-4 M6 Uncoated 12 0.108 Bladed 2-5 M6 Uncoated 22 0.198 Chipped 3-1 M10 ta-c 10.03 Abraded, still available 4-1 M10 Uncoated 2.9 Wear and chipping Note: * Two sets of M6 taps are determined by the National Tool Quality Supervision and Inspection Center; ** Two sets of M10 taps are tested by a large-scale tool factory test shop, and the cutting speed is 5.6m/min. 4 Application Assessment Shaanxi Bainer Co., Ltd. has coated amorphous diamond film high-speed steel cones for dozens of factories. The processing objects include 40Cr, 42CrMo, 30CrMo, 16Mn, free-cutting steel, gray cast iron, and titanium alloys. Tap Specifications From M1.5 to M20 and many others. Feedback from users showed that after the amorphous diamond film was plated, the service life of the tap increased by 0.67 to 4.56 times (see Table 5). Because the quality of the taps produced by different tool factories varies greatly, and the user's conditions of use and processing materials are different, the service life of the plated amorphous diamond film taps varies greatly. However, many users have reported that the lifetime of coated taps, which are worn out by wear, is more than double that of the coated taps that have failed due to wear. (The failure of the coated taps, which have improved their lifetime by less than 2 times, is mostly caused by chipping and breaking.) Table 5 User Usage Report No. Tap Size Process Target Coating Tap Life Un-Coated Tap Life Coating Tap Life-Restore Multiplier User Name Material Hardness 1 M6 HT200 240HB 16m 5m 2.2 Shenlong Automobile Co., Ltd. 2 M6 HT200 220HB 347 Hole 192 Hole 0.81 Standard Industrial Co., Ltd. 3 M12 HT200 220HB 15m 9m 0.67 Shaanxi Automobile Factory 4 M11 30CrMo 230HB 200 Hole 100 Hole 1.0 Baoji Machine Tool Plant 5 M3.5 Y12 200 Hole 65 Hole 2.08 Dongfang Machinery Plant 6 M7.5 Y15 229HB 5000 Hole 900 Hole 4.56 Qinghai Measuring Blade with Limit Company 7 M4 42CrMo 40HRC 24 Hole 10 Hole 1.4 Guanghua Numerical Control Tool Factory 8 M1.6 Titanium Alloy 20 Hole 5 Hole 3 Shaanxi Southwest Tool Co., Ltd. 5 Analysis and Discussion Overcome the failure of chipping and fully exploit the wear potential of coated taps The failure analysis showed that when the chipping failed, the unattached taps had serious wear on the adjoining tooth cutting edges and tooth tops (see Figure 2a). After the failure of the coated taps, the adjoining teeth had no signs of wear (see Figure 2a). See Figure 2b). This shows that the failure of the coating has not been exploited when it fails due to chipping. This is fully confirmed in the relationship between tap life and failure mode in tap performance test and user report. To overcome the chipping failure of the tap, it is necessary to improve the basic quality of the tap, that is, to improve the composition and metallurgical quality of the material (including carbide size, morphology, and distribution), and to improve the heat treatment and processing quality so as to improve the toughness of the tap and the fatigue crack initiation resistance. Reducing the notch sensitivity requires the joint efforts of steel mills and tool manufacturers. To prevent the temperature from rising, to protect the performance of the amorphous diamond film The amorphous diamond film will tend to have a graphitization tendency when the temperature is ≥600°C, that is, it is converted from the SP3 diamond structure to the SP2 graphite structure, the hardness and the film/base of the coating at this time. The binding force will be significantly reduced, so the temperature of the tap surface needs to be prevented from increasing during the operation of the coated tap. Taking effective cooling measures is beneficial for improving the cutting performance of amorphous diamond film taps. According to practical experience, if the tap temperature is less than 600°C and the long-term temperature is less than 500°C, or when the amorphous diamond-plated taps are processed not only for non-ferrous metals, but also for processing steel materials, they can effectively increase the life. High tap finish and high hardness improve the life of the tap. Because the amorphous diamond film is plated on the tap, the film thickness is only 150 ~ 200nm. If the tap surface roughness is not high accuracy, the convex point of the tap can easily collapse in the working process. The coating on it is no longer present, exposing the base material, and the overall wear resistance of the coating is lost. The wear resistance test shows that the higher the finish, the better the wear resistance of the coating. Nano-scale coating requires a hard substrate for support to prevent deformation and collapse during stress. Therefore, a moderate increase in the hardness of the substrate is beneficial to the wear-resistance potential of the coating. Of course, if the hardness of the substrate is too high, the toughness of the material will be reduced, and there will be a risk of chipping. Therefore, it is necessary to optimize the hardness of the substrate and balance it.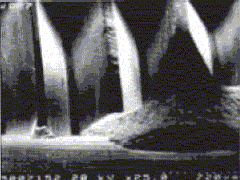
(a) M4 uncoated tap, failure of chipping, severe wear of adjacent unbroken wire edge and chipping tip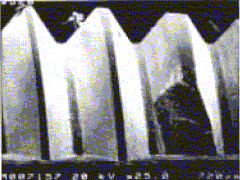
(b) M4 coated taps, chipping failure, no wear on adjacent thread edge and tip. Figure 2 6 Conclusion The amorphous diamond film has high hardness, low coefficient of friction, and good film-to-base bonding force. Has a high wear resistance. Shaanxi Baina Technology Development Co., Ltd. successfully developed a high wear-resistant tap and the user's production and use certification: the deposition of amorphous diamond film on the high-speed steel cone can significantly improve the service life of the tap, apply the coated tap to non-ferrous metals, The processing of steel and cast iron can achieve satisfactory results. In addition, Shaanxi Baina Co., Ltd. has also provided a large number of tools, gauges and molds for users to plate amorphous diamond films, which have significantly improved the service life.
Table 1 Basic properties of amorphous diamond film Amorphous diamond film Diamond (natural, crystalline) SP3 content, % 70 to 95 100 Hardness, GPa 70 to 95 100 to 120 Density, g/cm3 3 to 3.5 3.515 Young's modulus, GPa ≥700 1000~1200 Resistivity,Wcm 108~1012 1016 Thermal conductivity,W/cm2·K 18 20 Optical bandgap,eV 2.6 5.45 Tap is a widely used tool in mechanical manufacturing. In recent years, the annual consumption of taps in our country is about 40 million sticks, each tap tapping life of 3.5 ~ 4m, that is, high-quality products, the actual use of the tap life is often less than 3m, and the foreign tap life (≥ 10m) compared to a wide gap. In order to make domestic taps reach or close to the foreign product level, many manufacturers have made unremitting efforts to explore the material composition, metallurgy quality, heat treatment, processing technology, knife-like structure design and surface coating and other aspects, but with little success. Therefore, the domestic industry generally believes that TiN, TiC, TiCN, CrN, TiAlN and other coatings on the life of the tap does not have much gain, many manufacturers almost gave up the tap coating efforts. Shaanxi Baina Technology Development Co., Ltd. analyzed the performance characteristics and process characteristics of nano-amorphous diamond coating, and considered this coating suitable for tapping applications. At present, PLATIT company in Switzerland has diamond-like film taps, but its film hardness is low. Shaanxi Baina Company applied amorphous diamond film to high-speed steel wire cones and developed high wear-resistant taps, and applied assessments at several factories. This article focuses on the analysis of high-speed steel plated amorphous diamond film, film/base bonding force, friction coefficient, wear resistance test results and high-speed steel cone after coating performance test and practical assessment results, and put forward reasonable application and give full play to the amorphous Diamond film potential measures. 2 test program test material test material and tap material are W6Mo5Cr4V2 high-speed steel, heat treatment according to conventional high-speed steel heat treatment specifications; test piece size f20 × 5mm, roughness Ra0.4, grinding machine taps M3 ~ M12. Coating process sample pretreatment: Acetone ultrasonic cleaning → Washing → Deionized water washing → Alcohol cleaning → Blow drying, stored in a dry container for use. An amorphous diamond film was deposited on the test piece using a filtered cathode vacuum arc ion coating machine (JM-1 amorphous diamond coating machine) developed by Shaanxi Bainar Science and Technology Development Co., Ltd. and deposited under optimized parameters for 30 minutes. Test project coating and substrate binding force determination: With the WS-2000 type coating adhesion scratch tester, according to JB/T 8554-1997 standards to determine the critical layer rupture or peeling load. Each test piece was measured three times and the average value was taken as the film/base binding force of the test piece. Friction coefficient measurement: Using UMT-2M (bolt type) friction tester, the coefficient of friction of the film and steel ball was measured by reciprocating motion. Ball diameter f4mm, hardness 62HRC, load 2N, relative movement speed 18mm/s. Abrasion resistance test: According to the ISO 3160-3:1993 standard, a wear test was performed on a MS-2 type friction tester. The grinding head is a f8mm steel ball with a hardness of 61-64HRC, loaded with 2N, and a rotational speed of 120r/min. The number of revolutions at which a visible continuous wear scar appears appears as the wear life. Tap performance test: According to JB/T 969-94 standard tapping life test on Z525 vertical drilling machine. The blank was made of 40Cr, hardness 200-220HB, spindle speed 366r/min, cutting speed 6.9m/min, clamping accuracy 0.05-0.09mm, and emulsion cooling. Table 2 Coefficients of friction of amorphous diamond film (ta-c) and commonly used coatings Coated substrate friction coefficient Parameter source ta-c W6Mo5Cr4V2 0.092 Cr12MoV 0.098 TiN tool steel 0.55 Siemens PLATIT company TiCN 0.2 TiAlCN 0.5 CrN 0.3 TiAlCN 0.25 3 Test results and analysis of friction coefficient of amorphous diamond film The friction coefficient of high-speed steel W6Mo5Cr4V2 and mold steel Cr12MoV after coating is shown in Table 2. Also listed are the friction coefficients of several commonly used coatings for comparison. It can be seen from Table 2 that the friction coefficient μ of the plated amorphous diamond film and the ball steel ball on high-speed steel and die steel is 0.092-0.098, which is much lower than that of common hard coating. There are also many reports that the friction coefficient of amorphous diamond film μ ≤ 0.08, after a deep understanding of the test conditions, that the test head is an emerald ball, so the friction coefficient is lower than the test results. Since the amorphous diamond film is composed of a carbon-homo isomer SP3 and SP2 hybrid bonding structure having a low friction coefficient, and the film is extremely uniform, dense, and smooth, the amorphous diamond film has a very low coefficient of friction. , can be seen as a coating with self-lubricating function. The binding force between the amorphous diamond film and the substrate The results of the determination of the binding force between the amorphous diamond film and the high-speed steel substrate are shown in Table 3. As can be seen from Table 3, the highest critical load in the specimen is 22.75N and the minimum is 17.15N. The average critical load of the three specimens is 19.15N. Since the thickness of the coating is about 150 to 200 nm, such a thin coating is measured on a WS-2000 scratch tester, and the resulting data tends to be low. The binding force of amorphous diamond films on silicon, glass and steel is relatively high, which is mainly related to the process of nucleation and growth of amorphous diamond films by subsurface implantation. If the coating is a purely surface process, it usually has a lower binding force.
Table 3 Coupling force of amorphous diamond film and high-speed steel substrate Specimen No No critical load Lc(N) Average critical load L c(N) 1 20.40 20.27 22.75 17.67 2 18.10 19.52 18.15 22.30 3 17.15 17.65 17.77 18.02
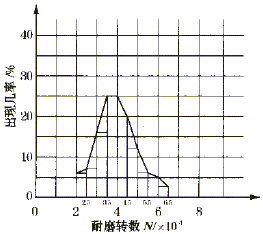
Fig. 1 Abrasion resistance of amorphous diamond film The wear resistance of the tracking plate of a high-speed steel cone coating (84 burners total) was tested on a MS-2 friction tester. The test results are shown in Figure 1. The minimum wear life of the coating was 21,410 rpm, the maximum life was 63,996 rpm, and the 30,000-50,000 rpm range accounted for 73.81%. This shows that the coating has good quality stability. The uncoated high-speed steel wear rotation is only about 200 rpm. Therefore, under the conditions of standard plug wear in the laboratory, the wear resistance of the high-speed steel plated amorphous diamond film increases by 106 to 319 times. Although the plated amorphous diamond film is very thin, its effect of improving the wear resistance is very remarkable. In general, the wear resistance of the coating depends mainly on the hardness of the coating, the coefficient of friction, the bonding force of the film, and the thickness of the film. Amorphous diamond film is a superhard film with a small friction coefficient. The film has a high bonding force and has high wear resistance despite the nanometer thickness. When we optimized the process, we found that if the film/base bonding force (critical load) is less than 10N, the wear resistance of the film is significantly worse. The results of the cutting performance test of the plated amorphous diamond film taps are shown in Table 4. The average cutting life of the amorphous diamond coated M6 tap was 5.6 times longer than that of the uncoated tap, and the mean cutting life of the coated M10 tap was 2.46 times longer than that of the uncoated tap. It can be seen that after tapping the amorphous diamond film on the tap, the service life of the tap can be effectively improved. It was also found in the test that the taps that failed in the wear mode had high cutting life, while the taps that failed in the chipping had shorter life spans. This shows that the wear resistance potential of amorphous diamond films can only be fully exerted when they fail due to wear.
Table 4 Cutting efficiency test results of plated amorphous diamond film taps No Tap size Coating life failure mode Number of holes (m) 1-1 M6 ta-c 186 1.674 Wear 1-2 M6 ta-c 187 1.683 Wear 1-3 M6 Ta-c 54 0.486 chipping 1-4 M6 ta-c 112 1.008 chipping 1-5 M6 ta-c 87 0.783 chipping, wear 2-1 M6 uncoated 30 0.27 chipping 2-2 M6 uncoated 20 0.18 collapse Blade 2-3 M6 Uncoated 8 0.072 Bladed 2-4 M6 Uncoated 12 0.108 Bladed 2-5 M6 Uncoated 22 0.198 Chipped 3-1 M10 ta-c 10.03 Abraded, still available 4-1 M10 Uncoated 2.9 Wear and chipping Note: * Two sets of M6 taps are determined by the National Tool Quality Supervision and Inspection Center; ** Two sets of M10 taps are tested by a large-scale tool factory test shop, and the cutting speed is 5.6m/min. 4 Application Assessment Shaanxi Bainer Co., Ltd. has coated amorphous diamond film high-speed steel cones for dozens of factories. The processing objects include 40Cr, 42CrMo, 30CrMo, 16Mn, free-cutting steel, gray cast iron, and titanium alloys. Tap Specifications From M1.5 to M20 and many others. Feedback from users showed that after the amorphous diamond film was plated, the service life of the tap increased by 0.67 to 4.56 times (see Table 5). Because the quality of the taps produced by different tool factories varies greatly, and the user's conditions of use and processing materials are different, the service life of the plated amorphous diamond film taps varies greatly. However, many users have reported that the lifetime of coated taps, which are worn out by wear, is more than double that of the coated taps that have failed due to wear. (The failure of the coated taps, which have improved their lifetime by less than 2 times, is mostly caused by chipping and breaking.) Table 5 User Usage Report No. Tap Size Process Target Coating Tap Life Un-Coated Tap Life Coating Tap Life-Restore Multiplier User Name Material Hardness 1 M6 HT200 240HB 16m 5m 2.2 Shenlong Automobile Co., Ltd. 2 M6 HT200 220HB 347 Hole 192 Hole 0.81 Standard Industrial Co., Ltd. 3 M12 HT200 220HB 15m 9m 0.67 Shaanxi Automobile Factory 4 M11 30CrMo 230HB 200 Hole 100 Hole 1.0 Baoji Machine Tool Plant 5 M3.5 Y12 200 Hole 65 Hole 2.08 Dongfang Machinery Plant 6 M7.5 Y15 229HB 5000 Hole 900 Hole 4.56 Qinghai Measuring Blade with Limit Company 7 M4 42CrMo 40HRC 24 Hole 10 Hole 1.4 Guanghua Numerical Control Tool Factory 8 M1.6 Titanium Alloy 20 Hole 5 Hole 3 Shaanxi Southwest Tool Co., Ltd. 5 Analysis and Discussion Overcome the failure of chipping and fully exploit the wear potential of coated taps The failure analysis showed that when the chipping failed, the unattached taps had serious wear on the adjoining tooth cutting edges and tooth tops (see Figure 2a). After the failure of the coated taps, the adjoining teeth had no signs of wear (see Figure 2a). See Figure 2b). This shows that the failure of the coating has not been exploited when it fails due to chipping. This is fully confirmed in the relationship between tap life and failure mode in tap performance test and user report. To overcome the chipping failure of the tap, it is necessary to improve the basic quality of the tap, that is, to improve the composition and metallurgical quality of the material (including carbide size, morphology, and distribution), and to improve the heat treatment and processing quality so as to improve the toughness of the tap and the fatigue crack initiation resistance. Reducing the notch sensitivity requires the joint efforts of steel mills and tool manufacturers. To prevent the temperature from rising, to protect the performance of the amorphous diamond film The amorphous diamond film will tend to have a graphitization tendency when the temperature is ≥600°C, that is, it is converted from the SP3 diamond structure to the SP2 graphite structure, the hardness and the film/base of the coating at this time. The binding force will be significantly reduced, so the temperature of the tap surface needs to be prevented from increasing during the operation of the coated tap. Taking effective cooling measures is beneficial for improving the cutting performance of amorphous diamond film taps. According to practical experience, if the tap temperature is less than 600°C and the long-term temperature is less than 500°C, or when the amorphous diamond-plated taps are processed not only for non-ferrous metals, but also for processing steel materials, they can effectively increase the life. High tap finish and high hardness improve the life of the tap. Because the amorphous diamond film is plated on the tap, the film thickness is only 150 ~ 200nm. If the tap surface roughness is not high accuracy, the convex point of the tap can easily collapse in the working process. The coating on it is no longer present, exposing the base material, and the overall wear resistance of the coating is lost. The wear resistance test shows that the higher the finish, the better the wear resistance of the coating. Nano-scale coating requires a hard substrate for support to prevent deformation and collapse during stress. Therefore, a moderate increase in the hardness of the substrate is beneficial to the wear-resistance potential of the coating. Of course, if the hardness of the substrate is too high, the toughness of the material will be reduced, and there will be a risk of chipping. Therefore, it is necessary to optimize the hardness of the substrate and balance it.
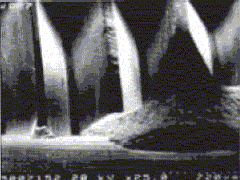
(a) M4 uncoated tap, failure of chipping, severe wear of adjacent unbroken wire edge and chipping tip
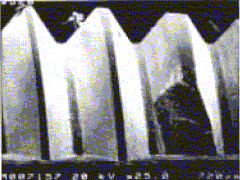
(b) M4 coated taps, chipping failure, no wear on adjacent thread edge and tip. Figure 2 6 Conclusion The amorphous diamond film has high hardness, low coefficient of friction, and good film-to-base bonding force. Has a high wear resistance. Shaanxi Baina Technology Development Co., Ltd. successfully developed a high wear-resistant tap and the user's production and use certification: the deposition of amorphous diamond film on the high-speed steel cone can significantly improve the service life of the tap, apply the coated tap to non-ferrous metals, The processing of steel and cast iron can achieve satisfactory results. In addition, Shaanxi Baina Co., Ltd. has also provided a large number of tools, gauges and molds for users to plate amorphous diamond films, which have significantly improved the service life.
* Mixer is the good friend of our dosing pump as it helps the dosing pump to mix the solution for the perfect flow rate.
* So normally the mixer will be needed in dosing system and it is as the necessary part for the device.
* Full power range of the mixer can be supplied, from 37W to 4kW.
* Special requiment of the shaft material can be get, such as SS304, SS316, SS line PTFE.
Kitchen Mixer,Powder Mixer,Liquid Mixer,Horizontal Mixer
Zhejiang Ailipu Technology Co., LTD. , https://www.alipu.com