In 2009, an ice disaster hit China's coastal areas, and a train carrying 20,000 tons of coal on the Daqin Railway was on the verge of death. This 5-km train was driven by only one motor train and one-stop direct transportation, breaking the “Guinness†record of the rail transportation industry at that time and making a sensation in the country. This initiative has enabled more people to understand the powerful power provided by China North Car Group Datong Electric Locomotive Co., Ltd. “High Power Heavy Loadâ€.
Daqin Railway is the first two-line electrified railway in China with heavy-duty unit trains. It is an important coal transportation channel for China's West Coal East. In 2009, an ice disaster hit China's coastal areas. The heavy snow and freezing rains cut off cables and electric towers in the past few days caused the power system to be interrupted. Moreover, the cold weather caused a sharp increase in electricity consumption and the supply of electricity was in short supply. These problems were given to the entire eastern region. The production and life have had a huge impact, and the supply of coal is imminent. It was solved by a train with a length of 5km and a coal consumption of up to 20,000 tons. The train was driven by only two 8-axle locomotives, which shocked the Chinese railway industry at the time, and this "super" The manufacturer of the train is not a foreign company, but the China North Locomotive Group Datong Electric Locomotive Co., Ltd. (hereinafter referred to as "Datong Locomotive").
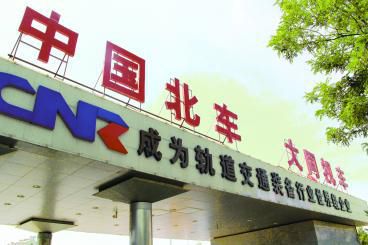
Established in 1954, Datong Locomotive has become the most complete locomotive manufacturer in China.
As a veteran state-owned enterprise established in 1954, Datong Locomotive has become the most complete locomotive manufacturer of electric locomotives in China. It not only has a national-level enterprise technology center, but also has a research and development base in the Beijing Economic and Technological Development Zone. After more than half a century of development, Datong Locomotive has developed and produced 14 types of electric locomotives, covering both DC drive and AC drive. Among them, the SS7C, SS7D and SS7E locomotives are the main locomotives for the third, fourth and fifth speed increase of the railway. From 2007 to 2009, Datong locomotive introduced the technology of Alstom in France, and jointly designed and produced Harmony Type 2 (HXD2) and Harmony 2B (HXD2B) high-power AC drive electric locomotives, representing the domestic AC drive electric locomotive. The highest configuration is the world's top electric locomotive products, reaching the international advanced level.
Datong locomotive has built and designed the 8-axis AC locomotive and the 6-axis AC locomotive design and manufacturing platform while introducing and digesting the advanced technology manufacturing technology of Alstom. It has invested a lot of money in the manufacturing methods and upgraded the equipment. And the technical transformation of the plant, the company has formed the production structure layout of the professional production of preparation materials, car body, frame, bogie, traction transformer, pantograph, modular electric panel cabinet, medium and high voltage electrical appliances, locomotive assembly and commissioning. The company digested and absorbed the advanced manufacturing management concept of Alstom, and successively implemented PDM, ERP, VPM system and CATIA three-dimensional design software, automatic sheet discharging and programming software, CNC machine tool DNC networking system, etc., and established a complete process technology standard. And process management standards, adhere to the use of advanced technology and standards to continuously improve and develop processes, and constantly move closer to international advanced technology and management systems. The process design of the company's various types of electric locomotives is carried out and managed in all PDM systems; the plate preparation (car body, frame, electrical panel) is all CNC typesetting; the key safety parts of the running department are all CNC machining or three-coordinate detection.
After the transformation of equipment and plane in recent years, especially after the addition of a large number of numerical control equipment, the processing and manufacturing capabilities of parts and components have been greatly improved, and in order to cooperate with new equipment, various technological equipments have been newly designed. At present, the company's annual production of electric locomotives (for example, 8-axis double-segment locomotives) has reached more than 500 units.
First-class transportation requires first-class equipment
In the same year, the Datong Qin Line 20,000-ton heavy-duty combined train traction operation task was the Datong locomotive Harmony Type 2 high-power electric locomotive. The locomotive was an 8-axis AC drive with a total power of 10,000 kW and a top speed of 120 km. The most powerful electric locomotive in the country represents the highest level in the world of heavy-duty fast freight.
Harmony 2 electric locomotive 20,000 tons of heavy-duty traction adopts "1+1" combined traction mode, that is, two locomotives draw 210 vehicles and 20,000 tons of coal for one-stop direct transportation for more than 10 hours. Harmony 2 electric locomotives started a 20,000-ton combined heavy-duty train, which greatly increased the transportation volume of Daqin Railway and greatly improved the transportation efficiency of the railway.
At present, there are more than 100 Harmony Type 2 electric locomotives participating in the transportation of 10,000 tons of cargo on the Daqin Line. The Harmony 2 locomotive has stable traction performance and excellent braking performance, demonstrating the first-class technology of heavy-duty traction of the locomotive, and all these achievements are inseparable from the support of the basic equipment behind it.
Datong Locomotive process development, product technology center Mr. Ren Panger primary wins
Pang Ersheng, director of the product development department of Datong Locomotive Technology Center, believes that equipment plays a decisive role in the manufacturing level of locomotives and directly affects manufacturing quality. The equipment mentioned here refers to various types of machine tools on the one hand, and various tool products involved in the process on the other hand. For the parts of rolling stock, the correct selection and use of the tools is sometimes more critical, and its quality and processing efficiency often become the primary factors that restrict the processing quality and delivery cycle of parts.
For sheet metal processing, sheet preparation includes car body, frame, electrical panel, etc. The steel plate of the car body needs to use the groove milling cutter for the bevel milling of the edge of the steel plate, and the precision requirement is Ra12.5. “The beveling of steel plates is mainly used for subsequent welding processes, so the accuracy requirements are not high, but there are strict requirements on the durability of the blades.†Director Pang said, “The continuous processing length of steel plates can sometimes Up to 14m, the tool can't be changed during the process, so there is a high requirement for the durability of the blade." Moreover, the output of the Datong locomotive is about 300 units a year, which is 600 cars, the processing task is heavy, and the processing efficiency is high. The requirements are very high.
In 2006, Datong locomotive got to know Walter, and Walter provided three non-standard tool products, namely F-2001-700346, F-2001-700348 and F-2001-700331, and the blade was ADKT16 0408. In the early days of cooperation with Alstom of France, Walter knives quickly realized the processing tasks of Datong locomotive sheet materials, which played a decisive role in the smooth delivery of Harmony Type 2 electric locomotives. These products are still in Datong locomotives. Serving in the workshop. This is only the beginning of cooperation between the two parties. In 2009, Datong locomotive once again cooperated with Walter on the processing of some parts in the frame. Since then, Walter's processing advantages have been fully demonstrated in the processing of Datong locomotives.
Life, accuracy, and efficiency
The bogie is a key component of the running part of the locomotive. It directly carries the weight and load of the car body, has a steering function, and ensures that the locomotive vehicle runs safely and smoothly on the track. The components that make up the bogie include wheel sets, axlebox devices, spring suspensions, base brakes, frames, bolsters, and more. In addition, the locomotive bogie also plays a driving role, and there are driving devices on the bogie of the motor car, such as a two-series spring suspension device.
As an important part of the bogie, the machining of the axle box becomes a top priority.
The Harmony 2 locomotive adopts an electric drive bogie. The traction motor mounted on the bogie generates torque through the transmission gear box to rotate the wheel pair. The rotating wheel pair generates traction of the locomotive through the adhesion between the wheel and rail. The locomotive traction force passes through. The axle box device is transmitted to the steering frame, and then transmitted to the vehicle body via the traction device, and then the train traction is realized by the coupler buffer device. The axle box device is connected with a series of suspensions, and its structural parameters have a direct impact on the running quality, energy consumption and component life of the locomotive. Datong locomotives have to manufacture more than 1,440 bogies a year, and there are 4 axle boxes on one bogie. A total of 5,760 axle housings are produced. Therefore, the machining efficiency of the axle housings becomes a key issue that challenges the processing capability of Datong locomotives. .
Mr. Fong locomotive shop technology machining a competent HU ZHIPENG demonstrate the use of tooling Walter shaft housing member.
According to Mr. Hu Zhipeng, technical director of Datong Locomotive Machining Workshop, since 2010, Datong Locomotives began to localize and manufacture locomotive bogies. As an important part of bogies, the processing of axleboxes has become a top priority. . “Especially, the requirements for tools are higher than ever. After comparison and multiple screenings, we used Walter's profiled end mills and taps.†Datong locomotives mainly use Walter's tools for the axle box. The machining of the parts is a processing of the R10 arc angle and the side hole of the axle box body.
Mr. Zhong Liyi, Technical Director of Datong Motorcycle Machining Workshop, showed the tool magazine equipped with Walter tools.
In the machining of the circular arc angle, the Walter F2231 copy milling cutter is used, and the machining part is two arcs of the front and the back. According to Walter Transportation Industry expert Chen Shenghua, the tool can simultaneously clamp two circular blades or combine the circular blade and the square blade. It can be clamped with a variety of handles, such as Moto taper or thread. Connect the system. The tool is mainly used for the processing of complex shapes in various industries. It is stable and safe and has high precision in profiling. Now the F2231 can be used with the Walter PVD series Tiger.tec and Tiger.tec Silver to make machining more efficient and better.
In the process of milling arc angle, using a profiling cutter Val Laid F2231, the processing site is both positive and negative circular arc.
The most impressive thing left to Hugong is the high durability of the Walter tap. On the two sides of the axle box parts, there are six sizes of M20, the accuracy grade is 6H, and the machining depth is 45mm. hole. "The processing requirements for them are first of all the machining accuracy of the tool, followed by the service life of the tool." Hu Gong clearly pointed out that "and for Walter's tool products, the most impressing us is the long tool life. Before the cooperation with Walter, all the machining tools will have a phenomenon, that is, the tool is chipping. This problem is fatal in the mass processing task, but the addition of the Walter tap solves the urgent need for the Datong locomotive. According to Hu Gong, now that the processing shop only applies one tap of Walter one day, it can complete the hole processing of the eight shaft boxes, and there will be no phenomenon of chipping in the middle. There are 12 holes in one axle box, so that one tap can process about 100 threaded holes per day. The efficiency is amazing!
Going to high-end manufacturing
Datong locomotive's axle box material is cast steel. At present, Datong locomotive is developing new gearbox products. In view of the successful cooperation with Walter, Datong locomotive still uses Walter's in the trial production process of new gearbox products. product. “The new gearbox material is cast iron, which is used in our company's newly designed model 30 tons of large axle weight electric locomotive. In October 2013, our workshop carried out trial production of the gearbox.†Hu Gong said, “The new product has deep hole processing. In the trial production process, we selected Walter's two extended drills with diameters of 11mm and 12mm for the oil return hole processing. The two holes have a depth of about 160mm, which belongs to deep hole machining. The ability of the pin is required, and the hole size and position tolerance are 0.5mm."
Gear oil is required in the gearbox, so the matching of each surface requires very high precision, and the sealing of the gearbox is guaranteed. The roughness of the surface processed using the Walter tool product is Ra3.2, and the roughness of the deep hole is Ra1.6. The current test results show that Walter's products can fully meet the demand. However, high-quality products are only one aspect of Walter's technical capabilities. "In the new product trial process, Walter also participated in the development of some process planning, including which processing technology can be used to maximize efficiency while the tool is The service life has also reached the highest, and so on." Hu Gongshen said with a sense of experience.
At present, Datong Locomotive is responsible for the production of all Harmony 2 locomotives in the country, including D2, D2B and D2C. Not only that, Datong locomotives continue to develop and manufacture new locomotives, constantly processing existing processes and processes. Make improvements. This kind of research and development enthusiasm is benefited from the strong support of basic equipment. In the future development of Datong locomotive, I believe that there will be more high-quality products and processes, and Walter will certainly be one of them.
Alnico (AlNiCo) is the first developed a permanent magnet is made of aluminum, nickel, cobalt, iron and other trace metals composition of an alloy.According to different production process is divided into sintered Alnico (Sintered AlNiCo), and cast aluminum nickel and cobalt (Cast AlNiCo).Product shape of the round and square. Sintered products limited to the small size, their production out of rough tolerance is better than the rough cast product can be better workability.
Alnico alloys can be magnetised to produce strong magnetic fields and have a high coercivity (resistance to demagnetization), thus making strong permanent magnets. Of the more commonly available magnets, only rare-earth magnets such as neodymium and samarium-cobalt are stronger. Alnico Magnets produce magnetic field strength at their poles as high as 1500 gausses (0.15 teslas), or about 3000 times the strength of Earth's magnetic field. Some brands of alnico are isotropic and can be efficiently magnetized in any direction. Other types, such as Alnico 5 and alnico 8, are anisotropic, with each having a preferred direction of magnetization, or orientation. Anisotropic alloys generally have greater magnetic capacity in a preferred orientation than isotropic types. Alnico's remanence (Br) may exceed 12,000 G (1.2 T), its coercivity (Hc) can be up to 1000 oersteds (80 kA/m), its energy product ((BH)max) can be up to 5.5 MG·Oe (44 T·A/m). This means that alnico can produce a strong magnetic flux in closed magnetic circuits, but has relatively small resistance against demagnetization. The field strength at the poles of any permanent magnet depends very much on the shape and is usually well below the remanence strength of the material.
Alnico alloys have some of the highest Curie temperatures of any magnetic material, around 800 °C (1,470 °F), although the maximal working temperature is normally limited to around 538 °C (1,000 °F).[4] They are the only magnets that have useful magnetism even when heated red-hot.[5] This property, as well as its brittleness and high melting point, is the result of the strong tendency toward order due to intermetallic bonding between aluminium and other constituents. They are also one of the most stable magnets if they are handled properly. Alnico magnets are electrically conductive, unlike ceramic magnets.
Alnico magnets are widely used in industrial and consumer applications where strong permanent magnets are needed; examples are electric motors, electric guitar pickups, microphones, sensors, loudspeakers, magnetron tubes, and cow magnets. In many applications they are being superseded by rare-earth magnets, whose stronger fields (Br) and larger energy products (BHmax) allow smaller-size magnets to be used for a given application.
Alnico Magnet,Alnico Magnets,Alnico V Magnets,Alnico Rod Magnets,Alnico 3,Alnico 5
Jinyu Magnet (Ningbo) Co., Ltd. , https://www.magnetbonwin.com