At present, domestic aero-engine manufacturers almost exclusively use titanium mandrel blades, fan blades and guide vanes in the manner of manual grinding and exhausting. The thickness difference between the inlet and exhaust sides of the blades is large, the consistency is poor, and the profile is inaccurate. The quality of the blades is not high. As the steam turbine industry gradually adopts the CNC belt grinding machine to process the blade profile and the intake and exhaust sides, the aero engine manufacturer has also put forward the requirements of using the CNC belt grinding process to enter and exit the edge. It is eager to pass the CNC belt grinding machine. Solve the problem of the manufacture of aero-engine blades for grinding and cutting. Based on the analysis of the characteristics of aerospace titanium alloy blades and the production practice, process test and verification analysis of different blade NC belt grinding, this paper summarizes several necessary conditions and corresponding countermeasures for the realization of CNC abrasive belt grinding of aviation titanium alloy blades. .
Difficulties in the grinding and processing of the intake and exhaust sides The manufacturing processes of the aero-engine blades and the steam turbine blades vary greatly. The former mainly adopts the molding method, and the latter mainly adopts the material removal method. The material of the steam turbine blade is mostly stainless steel. Generally, the radial surface of the blade is milled as a radial reference. The shoulder or the groove and the tip hole are used as the axial reference. Then the multi-axis linkage machine is used to process the blade body line, and finally the CNC is processed. Abrasive belt grinding and polishing is completed; aviation blades are generally made of titanium alloy precision forging and casting method to manufacture compressor blades, and diffusion alloy/superplastic forming (DB/SPF) method is used to manufacture titanium alloy wide-chord fan blades, and the blade profile is formed by mold molding. Assurance, the space error of the profile accuracy is not more than 0.15mm, and it is no longer processed after molding. It is directly used as the benchmark for the profile positioning fixture to process the blade root groove and the intake and exhaust sides. Therefore, the processing of aviation titanium alloy blades is mainly the processing of the inlet and exhaust sides. For the numerical control abrasive belt grinding, the processing difficulties have the following main aspects.
(1) The inlet and exhaust sides of the aeronautical blades are very thin, and the large fan blades are only about R0.3mm, and some of the small compressor blades may even reach the R0.1mm level. This makes it necessary to use a small contact force for grinding when grinding the belt, otherwise it is difficult to ensure the accuracy of the profile, which places high demands on the contact force control of the belt grinding device.
(2) The grinding allowance is uneven. Forged titanium alloy compressor blades and super-molded fan blades are generally forged by flashing or wire-cutting into the exhaust side (guaranteed string width), and then subjected to the in-exhaust edge grinding and polishing process. The machining allowance of the gas-edge fillet (or partial elliptical cross-section) is very uneven, as shown in the following figure: the red part is the outer contour of the blank, and the arc part is the theoretical curve of the inlet and exhaust side.
(3) Blade deformation problem. This problem and the uneven grinding allowance are similar problems. Forging titanium alloy blades and superplastic forming blades are all deformed at a certain temperature, and are deformed by the residual stress, especially the compressor blades, the magnitude of the deformation and the blade advancement. The thickness of the exhaust side is on the same level, reaching 0.1mm or more, which is too large compared with the space error of the general profile of the air blade of 0.05mm. It must be corrected.
(4) Benchmark problems, profile positioning, and consistency after blade clamping. Precision forged blades and superplastically formed blade profiles are very accurate, but are still coarse references, which is still relatively coarse compared to turbine blade milling benchmarks. As mentioned above, this clamping positioning error is equivalent to the blade deformation error in the order of magnitude, which is also an important factor that cannot be ignored, and must be solved by correcting the coordinate system.
In addition, when the intake and exhaust sides are ground, the cooling conditions are not good, the thin edge heat dissipation conditions are not good, and the vane inlet and exhaust sides are prone to ablation, which also brings certain difficulties to the blade inlet and exhaust side grinding; Superplastic forming fan blades, in addition to the intake and exhaust side, the profile also needs to be ground and polished, and there are problems such as uneven surface allowance and deformation error.
Key technology of blade numerical control belt grinding 1. Improvement of abrasive belt device Improve the unitized technology of CNC abrasive belt grinding device by steam turbine blade production practice, optimize control technology and six-axis linkage programming technology, accumulate blade CNC belt grinding process data. With the ever-reflecting requirements in production, improvements to the belt assembly are also ongoing, with major improvements including:
(1) The assembly structure of the low friction guiding mechanism of the belt mechanism is optimized to reduce the static friction of the guiding mechanism, improve the sensitivity of the floating belt mechanism, and improve the control precision of the contact force;
(2) Updating the low-resistance floating cylinder to improve the contact force control accuracy;
(3) Optimize the structure of the belt wheel train and improve the assembly process to improve the parallelism of the wheel axle axis, increase the envelope angle of the contact wheel belt, and improve the running stability of the high speed belt;
(4) Optimized the B-axis design, using the B-axis drive without backlash bearing reducer, improving the dynamic performance of the B-axis by more than 10 times, and expanding the B-axis swing range (accommodating the large bending variation of the fan blades);
(5) Optimize the C-axis design, adopt the split gear backlash, reduce the C-axis size and structure quality, and improve the C-axis accuracy and dynamic characteristics;
(6) Improve the overall protection of the C-axis and the belt mechanism, and basically ensure that the belt mechanism is free of cleaning and maintenance-free;
(7) Improve the rough machining programming method by lateral grinding to improve the blade processing efficiency;
(8) With the new material contact wheel, the life of the contact wheel is increased from 7 to 10 days to 15 to 20 days.
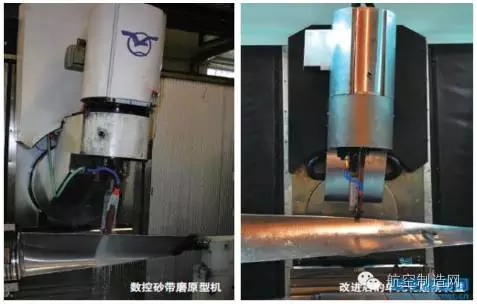
2, the static blade strong grinding test The purpose of the test is to verify the powerful grinding process and the surface precision control method through the powerful grinding of the turbine stationary blade.
Through the analysis of the characteristics of common static blade profiles, it can be seen that the surface distortion of the stationary blade is very small, even the barrel-shaped blade type, especially the blade without the crown, only the part of the blade body line (the first and last ends are cut after machining) The blade body line is very suitable for CNC belt grinding. For a six-axis linkage CNC belt grinding machine, it is feasible to select the appropriate contact wheel diameter, hardness and belt width. It is feasible to directly form the stator blade surface with strong grinding; and because the belt grinding speed is high, it has more milling than milling. High metal removal rate, direct grinding of the vane profile with powerful grinding, is superior to milling in terms of efficiency.
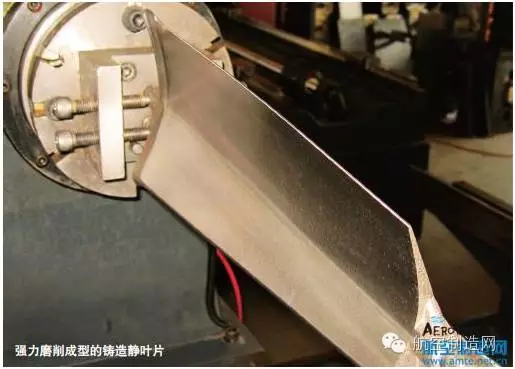
For aerospace titanium alloy blades, it is necessary to grind and cut the arc (or ellipse) of the intake and exhaust sides by sanding the grinding wheel; the key to ensure accurate line is to grind the contact force and improve the contact force control accuracy. Reducing the grinding contact force is the key to the accurate processing of the inlet and exhaust sides of aviation titanium alloy blades.
According to the characteristics of the aerospace titanium alloy blades mentioned above and the experimental research of several representative blade belt grinding, we can summarize the grinding of the aviation titanium alloy blade profile and the intake and exhaust side CNC belt under the process conditions. Several necessary conditions and existing countermeasures.
(1) Under the current process conditions, the manufacturing error of the aerospace titanium alloy blade blank profile and the intake and exhaust side are greater than the tolerance, and the CNC abrasive belt grinding is required to have the functions of correction, grinding and polishing, so the CNC abrasive belt grinding must be established. On the basis of the accurate measurement of the state of the blade clamping, that is, the machine tool must have the in-position measurement function (in-machine measurement), and the detection method should be as non-contact as possible, so as not to cause unnecessary when measuring the small blade of the compressor. Deformation. The possible method is CCD measurement or line laser scanning based on multi-vision principle. Considering the factors of blank reflection, current line laser scanning seems to have a slight advantage over CCD measurement.
(2) Based on the real-time and reverse-seeking rapid model reconstruction technology, the purpose of measurement is processing. It is necessary to quickly generate a model under realistic blank error or clamping difference state through model reconstruction, and judge whether it can process qualified. The product generates and corrects the machining program for processing. In the application of correcting the blade profile, it is inseparable from the support of model reconstruction and model comparison, otherwise it is not known where the machining is. Considering the blade processing efficiency, this process can be basically controlled to be completed in about 5 minutes.
(3) Partial correction function of abrasive belt grinding. Large deviations can be corrected by strong grinding and multiple theoretical passes, but for deviation corrections less than 0.1 mm, real-time pressure-controlled variable pressure grinding is more effective. At present, the experimental control of variable pressure grinding has been tested, and implementation is no longer a technical problem.
(4) Low friction guide and small contact force control are the key to achieve accurate machining of the inlet and exhaust sides of aviation titanium alloy blades. For R0.1mm grade inlet and exhaust edge grinding and polishing, the contact force may be less than 2N. To the grinding quality, the resolution of the contact force is not higher than 0.5N, and it is best to control it at 0.1N. This will challenge the belt mechanism guiding device. At present, the guiding device and the floating actuator can basically achieve zero friction. The rest is to reduce the quality of the belt floating mechanism and improve the motion sensitivity.
(5) Machine tool structure adapted to the structural characteristics of aviation titanium alloy blades. For forging blades and swept fan blades in compressor blades, the B-axis swing angle will be more demanding during machining, and the machine design should be fully considered; the large fan blades are twisted close to 90°, and the C-axis swing angle changes during machining. It will also be very large, and it is also the focus of the machine design.
Concluding remarks These are some of the experiences and conclusions of our work on the grinding of blade abrasive belts in the past three years. Many aspects still need further research, summarization, verification and refining to become the core technology of the profession. In recent years, many fields have been unable to meet the needs of domestic manufacturing in accordance with the usual introduction of technology, equipment and process. This is because domestic demand has reached international standards, such as three generations of nuclear power, new engine technology, and high-speed rail technology.
The implementation of major national special projects has undoubtedly provided strong support for the technical research that is urgently needed by the manufacturing industry. However, the implementation of special projects is staged and time-sensitive. The mastery and development of the core technologies of the manufacturing industry, the production, learning, and demand The close combination of research and use must become a normal state. The traction of this demand will not only change the product development model of equipment manufacturing enterprises, but may even affect the talent training mode of engineering colleges. We look forward to this change. With the research work of demand traction, it is not too far to solve the problem of the manufacture of aero-engine blades for the grinding and cutting of aviation titanium alloy blades.
Commodity name |
DIN933 Hex Head Bolt Full Thread Bolt Stainless Steel A2-70 |
Brand name |
Frico |
Main Standard |
DIN933/ISO4017 |
Material |
Stainless Steel |
Surface |
Self color |
Size |
Different size available ( M3-M48) |
M.O.Q |
10000pcs |
Packing |
Bulk packed(20-25kg)/ Small box then on pallet or according to customer`s requirements |
Delivery time |
30-35 days after the order confirmation |
Payment term |
T/T, L/C, Western Union |
Business type |
Manufacturer, trading |
Certifications |
ISO9001:2015 |
Advantage |
1. Competitive price; 2. OEM service available |
Notes |
Special specifications and marks can be made according to customers requirements; |
Main products |
Bolts, Screws, Nuts , thread studs, Anchors, lifting products, elbow, tee, reducer, plate flange, WN flange |
Special Fasteners,Professional Fasteners,Hot Forged Special Fasteners,Big Size Special Fasteners
Ningbo Brightfast Machinery Industry Trade Co.,Ltd , https://www.brightfastener.com