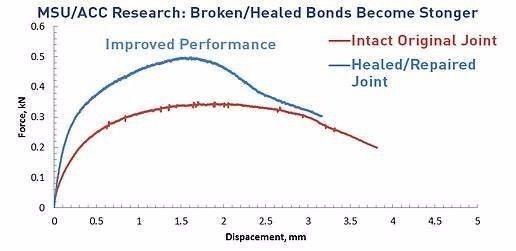
(Source: American Chemical Council) Studies have shown that a new type of "reversible" glue can make the bond after repair/reconnection more secure. A few days ago, researchers at the ACC American Chemistry Council and Michigan State University (MSU) demonstrated a new "reversible" multi-material joining adhesive. The special feature of this adhesive allows for a stronger bond after repair/reconnection, and this feature will greatly facilitate the maintenance and end-of-life recycling of a large number of carbon fiber reinforced materials (CFRP) models. During the Management Seminar (MBS) held in Traverse, Michigan, USA, Sandra McClelland, Automotive Business Development Manager of Solvay Specialty Polymers and current rotating chairman of the American Chemistry Council Automotive Working Group, said "This year, the researchers found that we can use this adhesive to bond parts, then separate the bonded parts, and finally do the second bond again, and the new connection after 'healing' is even better than the first time. The bond is stronger. This means that after the glue is repaired, a carbon fiber frame damaged in a car accident may be stronger than before the collision, and the vehicle with a mileage of 50,000 miles is repaired, and the carbon fiber frame of the vehicle is even better than It's even stronger at the factory." McClelland introduced the latest findings from Solvay and the Michigan State University's Composite Vehicle Research Center and Dr. Mahmoodul Haq in a reversible multi-material bonding collaborative research project. The development of this new adhesive is mainly to meet the automotive industry's multiple requirements for joining technology, including: the connection of different materials (plastic, steel, aluminum and composite materials), vehicle weight reduction, connection robustness (ASTM USA) Material and Test Association's structural efficiency test), bonding process completed in 45 seconds, and the connection process is reversible. That is to say, the bonded parts can be separated in the maintenance and repair process of the local depot, and "re-connected", so that the composite material recycling after the vehicle is scrapped will be more convenient and fast. At the management seminar, McClelland said that this "magic glue" is the joint research of the American Chemistry Council and Michigan State University, and it seems to meet the above requirements of the automotive industry. Another special feature of this thermoplastic adhesive is that the seams of the components to be joined can be completely joined together, rather than just a portion of the bond points. In addition, because the expansion stress at the joint is "very strong," manufacturers can significantly reduce the amount of this adhesive, resulting in additional vehicle weight reduction.
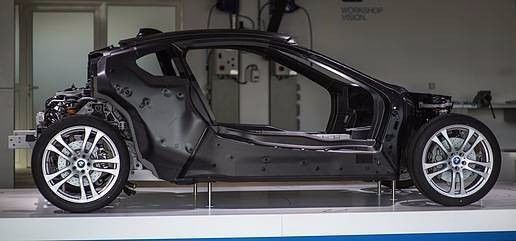
Reversible adhesives can play a huge role in vehicle maintenance and end-of-life recycling, especially for vehicles such as the BMW i8, which uses a large number of carbon fiber reinforced materials. (Source: BMW)
Reversible Process McClelland said that this thermoplastic adhesive can complete the complete process of melting, separation and reconnection in less than one minute, fully in line with the speed requirements of the assembly process plant for the bonding process. Specifically, the reversible adhesive contains a large amount of magnetic nano-iron microspheres that will vibrate when current passes through and rapidly heat up to a very high temperature (300 to 800° in a few seconds). Between F), thereby completing the melt separation process before the surrounding material begins to heat up. Since then, the adhesive can also harden in a matter of seconds, which is essentially a "quick-drying glue" that meets the needs of melt separation and re-bonding at any time. Researchers at Michigan State University first used a heated adhesive to attach a variety of different materials, and then failed tests on these joints and in accordance with ASTM Association against fatigue strength, shear stress, impact stress, flexural creep modulus, etc. The standard of the parameters is to evaluate the structural efficiency of these connections. The researchers then used the electromagnetic coil to re-melt the adhesive within 30 seconds and repeated the repeated test of the new connection after "healing". The data shows that the newly formed connections are stronger. McClelland said, "By melting the binder and re-giving it the energy it needs, the new joint crystallizes to a higher degree than before, and the degree of crystallization of the polymer can determine the strength of the polymer to some extent." McClelland added. R & D personnel will first try to reduce the cost of this adhesive, and then gradually commercialization, but no specific time plan has yet been developed. According to McClelland, "This adhesive has the characteristics of being more robust after repairing, and can solve the 'connection point' fatigue problem faced by the automotive industry to a certain extent."
Electric Angle Grinder
An angle grinder, also known as a side grinder or disc grinder, is a handheld power Tool used for grinding (abrasive cutting) and polishing. Although developed originally as tools for rigid abrasive discs, the availability of an interchangeable power source has encouraged their use with a wide variety of cutters and attachments.
Angle grinders can be powered by an electric motor or compressed air. The motor drives a geared head at a right-angle on which is mounted an abrasive disc or a thinner cut-off disc, either of which can be replaced when worn. Angle grinders typically have an adjustable guard and a side-handle for two-handed operation. Certain angle grinders, depending on their speed range, can be used as sanders, employing a sanding disc with a backing pad or disc. The backing system is typically made of hard plastic, phenolic resin, or medium-hard rubber depending on the amount of flexibility desired.
Electric Angle Grinder,lithium electric tool
Behappy Crafts (suzhou)Co.,Ltd , https://www.behappyindustry.com