Jinan Tianshan Seiko Bearing Co., Ltd. introduces the slack season and should take necessary maintenance for the nsk bearing submersible pump to extend the service life of nsk imported bearings and ensure normal use during busy hours:
1. Check the wearing parts: the impeller, retaining ring, bushing, bearing seat, etc. of the submersible pump are wearing parts. First, the pump part should be removed to check whether the wearing parts are intact. Damaged and unqualified parts are strictly prohibited.
2. Replace the lubricating oil: open the oil hole screw inside the sealing chamber and the motor separately, release all the lubricating oil inside the sealed chamber and the motor, replace the new oil, and ensure the normal operation of the lubrication system.
3. Demolition of the pump casing against rust: Before use in spring, the uppermost pump casing should be disassembled, and then the impeller should be turned and then closed to prevent the components from rusting and unable to start normally and burn the motor. This maintenance is especially important for water-filled motors.
4. Ensuring sealing: The requirements for sealing of agricultural submersible pumps are very strict. If oil is found to be turbid and the water content is high when replacing the lubricating oil in the sealed chamber, the sealing box or sealing ring must be replaced or replaced to ensure the sealing. Good performance.
5. Drying motor: measure the insulation resistance of the winding and the outer casing of the submersible pump with a 500 megohm meter. If the resistance is less than 0.5 megohm, the motor moisture should be removed. The drying methods include an external drying method, a current drying method, and a combined drying method in which both are performed simultaneously. The external drying method is to use external heat source for treatment. Commonly used measures are: (1) blowing hot air: a blower using an electric heater (a small submersible pump for agriculture can use a hair dryer) to blow hot air to achieve the purpose of drying treatment; (2) bulb baking: In a closed box, several 200 watt bulbs are used for baking. Note that the baking temperature should not be too high and should be controlled below 125 °C; (3) Current drying: The three-phase windings of the motor can be connected in series or in parallel according to the impedance of the submersible pump and the size of the power supply, and then a variable resistor is connected to adjust the current amount. It is about 60% of the rated current value and is energized and dried.
6. Ensure bearing lubrication: For the water-filled submersible pump, check the skeleton oil seal and lithium-based grease for the upper and lower end cap bearing chambers. To ensure that the bearing works in a well-lubricated state for a long time.
7. Check the bearing: Check the upper and lower bearings of the motor part. If it is found that the wear or the clearance is too large, the new bearing must be replaced in time. It is strictly forbidden to use the disease. The inspection method is as follows: If the motor is running, a “beep†sound is generated, and the cycle is proportional to the rotational speed, and it is laborious to rotate the rotor by hand, which is a little awkward or avulsive on the bearing race; if the bearing is intermittent The "beep" sound, there is an indeterminate dead point when turning the rotor by hand, usually the ball frame is damaged, the inner ring is broken or the ball is broken. In the above situation, the bearing must be replaced to avoid further damage.
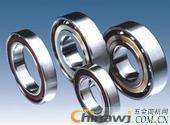
Standard:
ANSI B16.5,
EN1092-1 DIN2565 DIN 2566
Size: 1/2''~60''
Class Rating: 150~2500
Facing: RF(raised face);FF(flat face);RTJ(ring type joint);RJ(ring joint face)
TG(tongue and groove face);MFM(male and female face)
Manufacturing process: forge,
Material:
Carbon steel:
ASTM A105;
ASTM A266 GR.1,GR.2,GR.3,GR.4
Stainless steel:
304/SUS304/UNS S30400/1.4301
304L/UNS S30403/1.4306;
304H/UNS S30409/1.4948;
309S/UNS S30908/1.4833
309H/UNS S30909;
310S/UNS S31008/1.4845;
310H/UNS S31009;
316/UNS S31600/1.4401;
316Ti/UNS S31635/1.4571;
316H/UNS S31609/1.4436;
316L/UNS S31603/1.4404;
316LN/UNS S31653;
317/UNS S31700;
317L/UNS S31703/1.4438;
321/UNS S32100/1.4541;
321H/UNS S32109;
347/UNS S34700/1.4550;
347H/UNS S34709/1.4912;
348/UNS S34800;
Alloy steel:
ASTM A694 F42/F46/F48/F50/F52/F56/F60/F65/F70;
ASTM A182 F5a/F5/F9/F11/F12/F22/F91;
ASTM A350 LF1/LF2/LF3;
Duplex steel:
ASTM A182 F51/S31803/1.4462;
ASTM A182 F53/S2507/S32750/1.4401;
ASTM A182 F55/S32760/1.4501/Zeron 100;
2205/F60/S32205;
ASTM A182 F44/S31254/254SMO/1.4547;
17-4PH/S17400/1.4542/SUS630/AISI630;
F904L/NO8904/1.4539;
725LN/310MoLN/S31050/1.4466
253MA/S30815/1.4835
Nickel alloy steel:
Alloy 200/Nickel 200/NO2200/2.4066/ASTM B366 WPN;
Alloy 201/Nickel 201/NO2201/2.4068/ASTM B366 WPNL;
Alloy 400/Monel 400/NO4400/NS111/2.4360/ASTM B366 WPNC;
Alloy K-500/Monel K-500/NO5500/2.475;
Alloy 600/Inconel 600/NO6600/NS333/2.4816;
Alloy 601/Inconel 601/NO6001/2.4851;
Alloy 625/Inconel 625/NO6625/NS336/2.4856;
Alloy 718/Inconel 718/NO7718/GH169/GH4169/2.4668;
Alloy 800/Incoloy 800/NO8800/1.4876;
Alloy 800H/Incoloy 800H/NO8810/1.4958;
Alloy 800HT/Incoloy 800HT/NO8811/1.4959;
Alloy 825/Incoloy 825/NO8825/2.4858/NS142;
Alloy 925/Incoloy 925/NO9925;
Hastelloy C/Alloy C/NO6003/2.4869/NS333;
Alloy C-276/Hastelloy C-276/N10276/2.4819;
Alloy C-4/Hastelloy C-4/NO6455/NS335/2.4610;
Alloy C-22/Hastelloy C-22/NO6022/2.4602;
Alloy C-2000/Hastelloy C-2000/NO6200/2.4675;
Alloy B/Hastelloy B/NS321/N10001;
Alloy B-2/Hastelloy B-2/N10665/NS322/2.4617;
Alloy B-3/Hastelloy B-3/N10675/2.4600;
Alloy X/Hastelloy X/NO6002/2.4665;
Alloy G-30/Hastelloy G-30/NO6030/2.4603;
Alloy X-750/Inconel X-750/NO7750/GH145/2.4669;
Alloy 20/Carpenter 20Cb3/NO8020/NS312/2.4660;
Alloy 31/NO8031/1.4562;
Alloy 901/NO9901/1.4898;
Incoloy 25-6Mo/NO8926/1.4529/Incoloy 926/Alloy 926;
Inconel 783/UNS R30783;
NAS 254NM/NO8367;
Monel 30C
Nimonic 80A/Nickel Alloy 80a/UNS N07080/NA20/2.4631/2.4952
Nimonic 263/NO7263
Nimonic 90/UNS NO7090;
Incoloy 907/GH907;
Nitronic 60/Alloy 218/UNS S21800
Threaded flange is a flange that connects threads to pipes. When it is designed, it can be treated by a loose flange. The advantage is that there is no need for welding, and the additional torque on the cylinder or pipe when the flange is deformed is very small. The disadvantage is that the thickness of the flange is large and the cost is high. It is suitable for the connection of high pressure pipe.
The threaded flange is made from the inner hole of the flange into pipe thread and connected with the pipe with thread, which is a non welded flange. Compared with the flat welding flange or butt welding flange, the threaded flange has the characteristics of convenient installation and maintenance, and can be used on some pipelines which are not allowed to be welded on the spot. Alloy steel flanges are of sufficient strength, but they are not easy to weld or have poor weldability. Threaded flanges can also be selected. However, if the temperature changes rapidly or the temperature is higher than 260 C below -45 C, it is recommended not to use threaded flange to avoid leakage.
Threaded Flange,Din Thread Flange,Astm Threaded Flange,En1092-1 Thread Flange
HeBei GuangHao Pipe Fittings Co .,LTD (Cangzhou Sailing Steel Pipe Co., Ltd) , https://www.guanghaofitting.com