The efficiency of the three-screw pump is very important, and it is also the user's most concerned. How to improve efficiency?
Needless to say, what is the purpose of replacing equipment with equipment? It is efficiency! Therefore, in order to stand out, you must have higher efficiency than other peers. To do this, look at the ways to improve the efficiency of the three-screw pump:
(1) Improve the pumping capacity of the three screw
Now the most common mechanical oil recovery method is the three-screw pump pumping, eliminating the interference of the pump air and controlling the running time of the pump, so that the pump displacement matches the liquid volume flowing into the bottom of the well, which can improve efficiency and reduce cost. High yield of screw pumping oil.
 1. Control the displacement of the three-screw pump , which can be controlled by adjusting 4 kinds of numbers: plunger size, punching degree, pump stroke number, daily running time. Pumps of an unsuitable size are usually not replaced due to the high cost of the equipment. The easiest way to do this is to change the configuration of the ground equipment, such as moving the beam lever to change the stroke length of the ground and pump; the second is to replace the motor pulley to control the pump stroke. The matching of pump volume to well capacity can be achieved by changing the daily running time. The following devices can be used to control the running time: the air pump controller, the interval timer and the percentage timer. The air pump controller stops the pump if it detects that the pump is not fully charged. The timer controls the running time of the pump, which is cheaper and simpler to operate. The duration of the pump stop should be as short as the well pressure at the bottom of the well does not exceed 10% of the reservoir pressure. The operator can perform the above-mentioned sound wave and dynamometer measurement for 45 minutes for each well to determine the well productivity, downhole pump dynamics, downhole gas separator dynamics, sucker rod and beam pumping unit load, and motor dynamics. Through 45 minutes of analysis, operators can maximize well production and reduce operating costs.
 2. The indicator meter measures the percentage of the pump fullness coefficient, and the integrated data acquisition system can simultaneously obtain the motor power and the indicator data. One of the main uses of the dynamometer is to diagnose how the pump operates and analyze downhole problems. Applying the production level measurement combined with the dynamometer to see if the well is produced at maximum throughput, if the liquid column height is above the pump inlet depth, if the pump is not fully filled, and if the free gas is moving up the casing annulus.
 3. Diagnose low energy efficiency wells. The method of diagnosis is to determine the overall efficiency of the pumping system, while determining the total efficiency requires only measuring the power input to the prime mover, determining the downhole production pressure and accurate production test data. Generally, the total efficiency of the beam pumping system should be about 50%. If it is lower than this, its performance should be improved. Techniques to increase overall efficiency include maintaining high volumetric efficiency (pump specifications match wellbore injection, eliminating gas interference, pumping with an evacuation controller or timer) and replacing oversized motors.
 4. Separation of underground gas. Ineffective pump operation is often caused by gas interference and can be diagnosed by acoustic level measurement and dynamometer. It is best to place the pump suction port below the fluid inlet section and, if placed above, a gas separator. If the valve seat nipple is placed at least 10 ft below the bottom of the fluid entry section, effective gas separation may occur in the annulus, at which point the casing acts as a separator outer cylinder. However, well conditions often do not allow the pump to be placed below the fluid entry layer, and a downhole gas separator is contemplated. Conventional gas separators consist of a fluid inlet section (such as a perforation nipple), an outer cylinder (such as a section of tubing with a plug at the bottom), and a liquid-sealing tube at the bottom of the pump.
(2) Modification of mechanical seal structure of three-screw pump
   Through the modification of the mechanical seal structure of the three-screw pump and the rational selection of the rinsing liquid, the performance of the mechanical seal is improved, the problem of frequent leakage of the mechanical seal is solved, the maintenance and maintenance cost of the equipment is reduced, and the continuous and stable production of the device is ensured. Since the three-screw pump is at the bottom of the stripper, the corrosion of pipes and equipment, as well as impurities and recombination polymers are deposited at the bottom of the tower. The residual oil entering the three-screw pump contains a large amount of impurities and polymer, and the amount of flushing is insufficient. These impurities and polymers are inevitably deposited in the sealed cavity, causing the gap between the moving ring and the moving ring seat and the bushing to be blocked, resulting in the movement of the moving ring in the axial direction being inflexible or even stuck, and the spring is stuck.涩, can not provide the original design of the end face specific pressure of 0.586MPa, resulting in the sealing surface can not be well adhered, the liquid film balance is destroyed, then the seal will appear micro-leakage, as the polymer and impurity particles enter the friction end face, seal The surface is gradually worn, and the axial compensation of the moving ring is not working, resulting in an increase in the amount of leakage of the seal, which eventually leads to complete failure of the seal.
   According to the failure reason of the seal, we have made technical transformations from the following aspects: According to the specific working conditions of the three-screw pump, we selected the Aizhi 318 type single-end mechanical seal (package type). The main features are as follows: precise centering is achieved by automatic locking ring. The adjustable gland can be directly used with common bolts, and the assembled structure is easy to install. The spring is located outside the auxiliary seal and is completely separated from the media to avoid spring jamming. The moving ring adopts the whole floating non-inlaid, and the static ring is designed by computer, and the z-shape is designed. The advantage is that the heat dissipation is good and the heat is not suitable for accumulation.
(3) Daily maintenance precautions for various pumps
1. Water will corrode the oil pump, so it is forbidden to use the oil pump to pump vacuum.
2. For substances containing a large amount of solvent, first remove most of the solvent in the oven, then use an oil pump to evacuate.
3. Use the vacuum pump in the correct order to prevent back suction.
4. After using the vacuum oven, be sure to clean it and wipe the glass window of the vacuum oven.
5. Wipe the surface anti-rust oil.
6. Remove the anti-rust oil from the inner chamber of the governor and the inner chamber of the fuel injection pump, and add the lubricating oil of the specified grade.
7. The anti-rust oil in the fuel line should also be removed before use. Connect the fuel to the fuel injection pump line and continuously rotate the injection pump camshaft until the outlet valve is clean and ignited.
8. The fuel selection is reasonable.
9, must use the appropriate fuel. Normally, No. 0 diesel is used in summer and No. 10 light diesel is used in winter.
10. The fuel used must be clean and must not contain any impurities or moisture.
This article comes from http://kpslgb.cn.gongchang.com/news.html, reproduced is please indicate the source, thank you for your cooperation!
Label: three screw pump
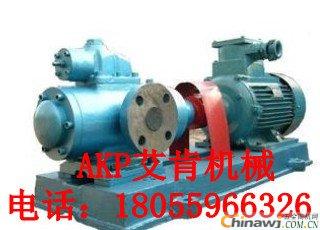
New design ceiling fan,ceiling fan with light,decorative ceiling fan
JIANGMEN ESCLIGHTING TECHNOLOGY LIMITED , https://www.jmwindfansummer.com