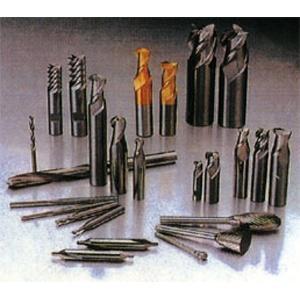
Improvement of mature processing methods With the increasing pressure of competition in the manufacturing industry, large-scale production of slender screws (such as bone screws) for high-performance metal materials is also increasing. Suppliers in the medical industry are often faced with this situation. Among them, the processing volume of such products is increasing, and thread whirling is a mature processing method. The inherent stability of this process makes it ideal for mass production and processing of demanding metals. A more solid cutting edge can be used for whirlwind milling, which provides more possibilities for the introduction of new tool materials with higher wear resistance.
The benefit is the longer tool life, which means shorter machine downtime in production. In addition, the edge line toughness of the cutting edge is improved, making the cutting edge more sharp and safer when cutting. The rational use of these technological advances in other processing areas has led to the development of special indexable inserts and knives suitable for small part cyclone milling, thereby consolidating the economic advantages of manufacturing medical parts.
The continuous development of blade technology provides more room for improved cutting edges to take full advantage of the benefits of thread whirling methods. For example, coated carbide inserts can achieve longer and more predictable tool life, and can apply higher cutting speeds. This leads to higher part yields and consistent tolerances and surface finishes. The new insert material (eg material with PVD/TiAlN coating) has a unique thin coating that provides excellent adhesion to the insert matrix. This material is ideally suited for the machining of various workpiece materials for thread whirling (such as those used for bone screws).
In the case of thread whirling, operational safety and tool clamping are also critical to ensure a higher processing performance. The tool accuracy determines the positioning of the blade, the quality of the blade grinding, and the convenience and reliability of each correct positioning of the blade. The newly developed insert clamping concept for thread whirling tools improves the positioning accuracy and processing safety of the cutting edge, and makes tool change on the machine tool easier and faster. The smooth tangential cutting action ensures the high precision and surface finish required throughout the machining process.
Currently, thread whirling tools should include specially developed sharpening inserts and semi-finished products, and should be compatible with most types and configurations of sliding toolholder spindles. Although mass production has a well-established process flow, meeting new demands for higher production and new parts also requires new processing techniques, such as the more advanced tool ring concepts in thread whirling.
In an example where thread screws are used to make bone screws, there are approximately 500,000 productions per year, and small batches will vary depending on the circumstances. After the installation of advanced indexable insert tools, not only reduce the processing costs, but also greatly enhance the manufacturing competitiveness. This new tool means that the tool life is extended by 9 times, and more parts can be machined before the cutting edge needs to be replaced (where the part size is about to exceed the tolerance). In addition to eliminating all machine downtime, tool maintenance time is greatly saved due to easier tool maintenance.
Advanced Coolant Applications Solve the Problem Now, slitting machines with coolant supplies can provide new possibilities for improving the machining of small parts. The use of a high pressure cooling system to replace the traditional cutting zone coolant flow has many processing advantages. The introduction of this auxiliary cutting tool does not require complicated and elaborate equipment, because standard tools can be used and internal cooling is common practice. High-pressure cooling processing has been continuously researched and developed over a period of time, which has resulted in today's high-level machining concepts. In the processing of demanding materials for chip control (such as superalloys and low carbon steels), the greatest advantage of this solution lies in improved processability and chip removal.
At present, new machining concepts can be applied when machining small parts, and the high-pressure coolant is directly and accurately injected into the cutting zone. This type of solution combines the precise orientation of the coolant injection and the simple and safe clamping of the shank. This opens up a whole new perspective for more efficient processing of demanding materials, especially on slitting machines, where small groups of tools are located in a very narrow space, making tool change and mounting difficult and time consuming. With a tool positioning and locking function and a machine equipped with a coolant connector, the new tool holding system can simultaneously improve machining and tool change capabilities.
Turning tools with High Pressure Cooling (HPC) features typically have three nozzles that accurately deliver the coolant jet to the blade in the right place. The coolant affects the distribution of heat generated in the cutting zone, the amount of tool wear, the actual shaping of the chip, and the degree of adhesion of the workpiece material attached to the cutting edge. Coolant injection effectively reduces the chip contact length by forming a so-called "hydraulic wedge" between the chip and the rake face of the insert. It has been confirmed that this has a great influence on tool life and chip formation. Achieving good chip control in the machine tool helps to ensure safe unattended production and tolerances and surface finish levels of machined parts and thereby increase production efficiency.
The use of a high-pressure cooling system on a machine suitable for machining small parts is very easy and tool change can be achieved quickly and easily. Only one screw and a spring-loaded wedge for holding the tool holder in the tool holder can be used to achieve this by clamping and releasing the holder. When the tool holder is installed and replaced, precise and safe cutting edge positioning can be achieved. In combination with internal cold in the tool holder and a simple and safe coolant joint between the tool holder and the tool holder, long chip material that is difficult to machine without faults can be used as a cutting method that can be commonly used when machining small parts in the medical industry.
A single screw on the QS-HP Quick Change shank can be used to perform a tool change. This usually results in a 2/3 or more change of tool change time – from 3 minutes to 1 minute. Clamping the wedge ensures that the extraction tool is safe and quick, and reduces the risk of the tool falling during clamping. Once the tool is mounted on the machine, the position of the cutting edge is automatically adjusted by the contact between the short shank and the stop. When performing front and back car operations, the safe cutting edge position generally reduces the tool movement by an average of 30%, thereby achieving the goal of improving accuracy.
Recent developments in cutting tools have made the Coro MIll325 thread whirling tool a more advantageous threading method. The use of thread whirling milling thread efficient and safe, and high precision. The new tool concept and indexable inserts have considerable advantages for machining small parts such as bone screws.
Turning with high-precision coolant injection has made great progress in various processing applications. This technology is now not only seen as a tool for solving problems, but also as a means to really optimize the performance of a large number of parts in the medical industry. When turning small parts, the CoroTurnQS-HP is able to apply high-pressure cooling functions and achieve fast and safe tool changes.
Liang metalworking Tools Co., Ltd. has more than 200 employees, who have undergone professional technical training and rich production technology experience. The company has self-supporting import and export rights, and more than 90% of its products are exported to Italy, More than 60 countries and regions, including Spain, the Netherlands, Poland, Russia, Nigeria, India, Iran, South Africa, Japan, Brazil, ELDOR, etc
5M Tape Measure,Metal Measuring Stick,Tape Rule Measurement,Long Steel Measuring Tape
Henan Liangjin Tools Co.,Ltd , https://www.jtapemeasure.com