According to the process requirements, the building gypsum production line is usually divided into five parts, namely the crushing system, the grinding system, the calcining system, the storage conveying system and the electronic control system.
Broken system:
The gypsum raw material enters the crusher via a feeder, and the crusher breaks the large-sized gypsum ore into small pieces of less than 30 mm for use. According to the size of gypsum raw materials and different production requirements, you can choose the crusher of the corresponding specifications, usually choose PE jaw crusher, cone crusher or PF impact crusher. In order to protect the environment, it can be equipped with dust removal equipment to meet environmental emission requirements.
2. Material transportation:
The crushed gypsum raw material is transported to the storage bin through the hoist for use. The storage bin is designed according to the requirements of material storage time to ensure a stable supply of materials. At the same time, the material turnover of each part is hoist, reducing the floor space.
3. Grinding system:
The gypsum raw material in the storage bin is processed into a gypsum mill by a vibrating feeder for finishing. An electromagnetic vibrating feeder is arranged under the storage bin. This device is interlocked with the mill to adjust the supply of the material according to the running condition of the mill. Materials are uniformly electromagnetic vibration feeder is continuously fed into the mill, grinding. The ground gypsum powder is blown out by the air blown by the mill blower and classified by an analyzer above the main machine. The powder with fineness conforms to the specification, enters the large cyclone collector with the wind flow, and is discharged after being discharged through the powder discharge tube. The finished product falls into the screw conveyor and is transported to the next system for calcination. The wind flow flows into the blower from the return duct of the large cyclone collector. The entire air duct system is closed and flows under negative pressure. Since the material to be ground contains moisture and evaporates into gas during the grinding process, the amount of air in the circulation air path increases, and the increased air volume is introduced into the bag from the pipeline between the large cyclone collector and the blower. Remove dust from the air and drain it to the environment to ensure a clean environment. The material of the grinding system is changed from the particle size of 0-30mm to 80-120 mesh, which meets the requirements of gypsum powder fineness.
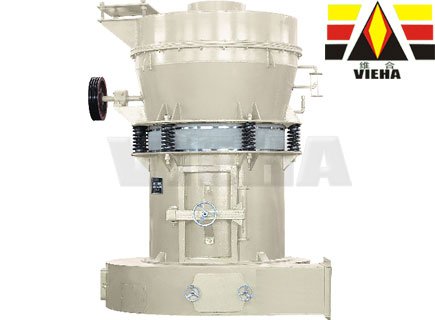
This RFID Fabric Wristbands popular with NXP Ntag213 chip inside, which would be read by all NFC devices, also can replaced by Ntag215, Ntag216 or any chip you need.
And are super easy to put on your wrist, look great with YOUR logo on a sliding PVC tag, and close with a white plastic clasp that has teeth to prevent the wristband from falling off.
And very popular using in music festival, a theme party, days ticket and so on.
The white plastic clasp on RFID Fabric Wristbands made for ONE-TIME USE only. There have reusable clasp too.
RFID Fabric Wristbands can be embedded 125Khz chips like Tk4100, EM4200, T5577, EME44305 and Hitag etc.
RFID Fabric Wristbands can be embedded 13.56MHZ chips like Ntag213, NTAG215, NTAG216, Mifare Classic, Desfire EV2/EV2, Plus X, Plus SE, ICODE, Ultralight, TI 2084, Topaz512, and F08 etc.
RFID Fabric Wristbands can be embedded 860MHZ-960MHZ chips like Alien H3, Alien H4, U-Code Gen2 and Impinj M4/M5 etc.
Special project? Custom RFID Fabric Wristbands? If you need more than 500 wristbands, you'll receive an instant discount!
Fast lead time and custom service, high quality and best price!
RFID Fabric Wristbands
RFID Fabric Wristbands,Fabric Wristbands,Custom Fabric Wristbands,Waterproof Fabric RFID Wristband
Sunway Smartech Co.,LTD , http://www.sunwayrfid.com