Introduction: There are specific requirements for the material of the furnace arch, the first is high temperature resistance. Because the furnace arch works at high temperatures for a long time, it directly contacts high-temperature flue gas, high-temperature ash slag and flame, which requires the material of the furnace arch to have sufficient High temperature resistance without melting, while having the ability to withstand the erosion of ash. The second is thermal shock stability. When the boiler starts up to full-load operation, due to improper operation, it may heat up too quickly, or suddenly stop at normal full load. At this time, the temperature of the front and rear arches changes greatly.
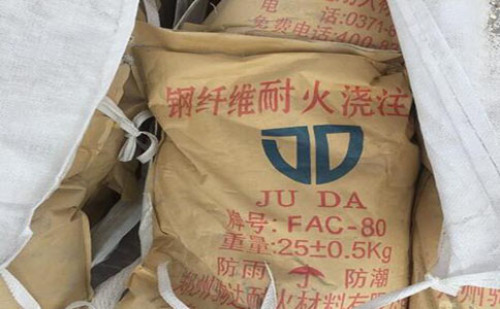
The chain furnace is a front-mounted furnace. The combustion process of coal is completed during the movement. It has stable combustion conditions, high thermal efficiency, convenient operation and operation, low labor intensity, and low dust emission concentration. It belongs to the single-sided fire work method, the fuel does not have its own disturbance during operation, along the length of the grate, the fuel layer has obvious partition. Most of these types of furnaces are used in the northwestern regions of China and heating companies in the northeast region are generally used in large quantities. Because of the high thermal efficiency of the chain boilers, coal-fired conditions have been used effectively, so they are widely accepted by the industry. The coal-fired chain boilers are not The good drawback is that the fire must be manually operated, so it is not suitable for burning coal with large moisture content, high ash content, and strong coking property.
The ignition point of the coal-fired chain boiler is mainly in the front section of the boiler. If the furnace arch design fails to cooperate, a lot of heat will be lost. Therefore, the furnace arch of the chain furnace is an important part of the entire furnace type. The furnace arch of the chain boiler is divided into front arches and rear arches, forming a combustion space together with the grate. Front arch (radiation arch): Located in the front of the grate, the main role is to ignite. Absorb radiant heat from flames and high-temperature flue gas, and radiate to new coal, then warm it up and catch fire. Rear arch: The main function of the rear part of the grate is to guide the high-temperature flue gas. There are about two types of flow-shaped furnace arches. The first one is that after the mixed combustion, the arch transports oxygen-rich flue gas to the front arch area. Mixed with combustible gas there. The front arch is generally short, the rear arch has a long gas transmission path, and the rear arch flue gas has a high flow velocity, resulting in a large mixture of disturbances. From the mixing point of view, the effect of the rear arch is dominant. The second is the role of insulation and stimulating: the rear arch can effectively prevent the grate from facing the upper part of the hearth, which can effectively increase the furnace temperature at the rear of the grate and play a role in insulation and combustion.
Therefore, the furnace arch is a key point of the chain boiler, and the material of the furnace arch has specific requirements, one is high temperature resistance. Because the furnace arch works at a high temperature for a long time, it is in direct contact with high-temperature flue gas, high-temperature ash slag, and flame. This requires that the material of the furnace arch has sufficient high temperature resistance without being melted, and at the same time has the ability to withstand the ash residue. The second is thermal shock stability. When the boiler starts up to full-load operation, due to improper operation, it may heat up too quickly, or suddenly stop at normal full load. At this time, the temperature of the front and rear arches changes greatly. Due to quenching and rapid heating, the internal stress generated inside the furnace arch can cause damage to the arch. The main factors affecting the stability of thermal shock are the coefficient of linear expansion and the coefficient of thermal conductivity. Materials with smaller linear expansion coefficients have higher thermal shock stability. The material with larger thermal conductivity has a stronger ability of absorbing heat and releasing heat when the temperature changes abruptly, and can reduce the internal stress of the arch, so the thermal shock stability is good. The third is the strength requirements of castable refractory. When the boiler is running, there is a fluctuation of the pressure caused by the unstable combustion in the furnace, and even a sudden explosion of the furnace arch receives a great deal of pressure, so the material must have a certain strength. The fourth is slag resistance. Resistance to chemical and physical effects of slag at high temperatures should be taken into account when selecting materials. Fifth, the weight of the material. The bulk density of the material is directly related to the carrying capacity of the furnace arch, the thermal conductivity of the material, and the compressive strength.
In summary, the refractoriness of masonry furnace arch must be above 1550°C, long-term use temperature is between 1100 and 1400°C, and the coefficient of linear expansion is small, thermal conductivity is good, thermal shock stability is strong, and it has certain mechanical strength. Fireproof castable. There are more similar materials from the high-grade materials that are distinguished from the price of corundum wear-resistant castable silicon carbide wear-resistant castable materials, but the higher cost price are at 5,000 yuan / ton up.
According to past experience, steel fiber wear-resistant castables are used, in which the stability of the material properties is good. The special grade bauxite clinker is used as aggregate, and the special grade bauxite clinker is used as the matrix. Superfine powder and other composite materials are binders and additives, plus stainless steel heat-resistant fibers. In addition to the conventional high-temperature wear resistance, the product incorporates a certain amount of heat-resistant stainless steel fiber in its ingredients to prevent the rise of aggregate and matrix in the material at high temperatures, as well as in the start-stop furnace. The stress generated by the change in the temperature gradient causes a drastic change in the damage. At the same time, due to the addition of steel fibers, the overall strength of the furnace arch is greatly enhanced after the material is poured. In the boiler, the use effect is better. Cutting cost is reasonable.
Black Wire: Black wire, also known as black annealed wire, is a type of wire that has undergone an annealing process to make it softer and more flexible. It is typically made from low carbon steel wire and has a black or dark gray appearance. Black wire is commonly used for tying, bundling, and securing purposes in construction, agriculture, and general applications. It is known for its malleability and ease of use.
Loop Tie Wire: Loop tie wire is a type of wire that is preformed into loops or ties for easy and efficient tying applications. It is often made from galvanized or black annealed wire. Loop tie wire is commonly used in construction, such as securing rebar, connecting WIRE MESH panels, and bundling construction materials. The preformed loops allow for quick installation and provide a secure and reliable connection.
Annealed Double Loop Tie Wire: Annealed double loop tie wire is a specific type of loop tie wire that has undergone an annealing process to make it softer and more pliable. It is typically made from black annealed wire. The double loop design consists of two preformed loops on opposite ends of the wire, allowing for easy and secure fastening. Annealed double loop tie wire is commonly used in construction, gardening, and other applications where quick and reliable tying is required.
Iron Binding Wire: Iron binding wire, also known as baling wire or tie wire, is a type of wire that is commonly used for binding, bundling, and securing various materials. It is typically made from galvanized or black annealed wire. Iron binding wire is widely used in construction, agriculture, packaging, and other industries. It provides strength, durability, and flexibility for applications such as securing packages, tying rebar, and fastening materials together.
These different types of wires, including black wire, loop tie wire, annealed double loop tie wire, and iron binding wire, offer solutions for various tying, bundling, and securing needs. The specific choice depends on factors such as the application, required strength, flexibility, and desired appearance.
Black Wire,Loop Tie Wire,Annealed Double Loop Tie Wire,Iron Binding Wire
Hebei Aibuer trading co., Ltd , https://www.ablehardwares.com